Have you ever come across the term "Russian lathe accident video" and wondered what it entails? These videos have gained significant attention online, often serving as a stark reminder of the dangers associated with operating industrial machinery. While they may seem shocking, they also provide valuable lessons on safety and risk management in the workplace. The keyword "Russian lathe accident video" has become a focal point for discussions about workplace safety, industrial hazards, and the importance of adhering to safety protocols. In this article, we will delve deep into the topic, exploring the causes of such accidents, the lessons we can learn, and how to prevent them in the future.
Industrial accidents, particularly those involving lathes, are not uncommon. Lathes are powerful machines used in various industries, from manufacturing to metalworking. However, their power and precision come with inherent risks if not handled properly. The videos showcasing these accidents often go viral, not just because of their shocking nature but also because they highlight the critical importance of safety measures. Understanding the risks and implementing proper safety protocols can save lives and prevent injuries.
In this comprehensive guide, we will explore the causes of lathe accidents, the role of human error and mechanical failure, and the steps that can be taken to ensure safety in industrial environments. We will also discuss the broader implications of these accidents, including their impact on workers' lives and the industries they serve. By the end of this article, you will have a clear understanding of the risks associated with lathe operations and how to mitigate them effectively.
Read also:Hafthor Bjornsson The Untold Story Of The Mountain
Table of Contents
- Understanding Lathe Accidents
- Causes of Lathe Accidents
- Human Error in Lathe Operations
- Mechanical Failure and Maintenance
- Safety Measures for Lathe Operators
- Case Studies of Lathe Accidents
- Legal and Industrial Implications
- Preventive Measures and Training
- The Role of Technology in Safety
- Conclusion and Call to Action
Understanding Lathe Accidents
Lathes are versatile machines used to shape materials such as metal, wood, and plastic by rotating the workpiece against a cutting tool. While they are essential in manufacturing and metalworking, they also pose significant risks if not operated correctly. Lathe accidents can result in severe injuries, including amputations, fractures, and even fatalities. Understanding the nature of these accidents is the first step in preventing them.
One of the most common types of lathe accidents involves entanglement. This occurs when loose clothing, jewelry, or long hair gets caught in the rotating parts of the machine. The force of the lathe can pull the operator into the machine, leading to catastrophic injuries. Another frequent cause of accidents is improper tool handling. Using dull or damaged tools can cause the workpiece to break loose, creating a dangerous projectile.
It is also important to note that lathe accidents are not limited to inexperienced operators. Even seasoned professionals can fall victim to these incidents if safety protocols are ignored or overlooked. This highlights the need for continuous education and vigilance in industrial environments.
Causes of Lathe Accidents
Lathe accidents can be attributed to a variety of factors, ranging from human error to mechanical failure. Below are some of the most common causes:
- Human Error: Mistakes made by operators, such as improper setup or failure to follow safety guidelines, are a leading cause of accidents.
- Mechanical Failure: Poorly maintained machines or defective parts can malfunction, leading to dangerous situations.
- Lack of Training: Inadequate training can leave operators unprepared to handle emergencies or recognize potential hazards.
- Improper Use of Tools: Using the wrong tools or failing to maintain them can increase the risk of accidents.
- Environmental Factors: Poor lighting, cluttered workspaces, and other environmental issues can contribute to accidents.
Understanding these causes is crucial for developing effective safety measures and preventing future incidents.
Human Error in Lathe Operations
Human error is one of the most significant contributors to lathe accidents. This can include mistakes such as failing to secure the workpiece properly, using incorrect tool settings, or neglecting to wear appropriate personal protective equipment (PPE). Even experienced operators can make errors, especially if they become complacent or distracted.
Read also:Lego Racers The Ultimate Guide To Building Racing And Collecting
To minimize the risk of human error, it is essential to implement strict safety protocols and provide ongoing training. Operators should be encouraged to double-check their setups and remain vigilant at all times. Additionally, fostering a culture of safety in the workplace can help reduce the likelihood of accidents.
Mechanical Failure and Maintenance
Mechanical failure is another common cause of lathe accidents. Machines that are not properly maintained can develop issues such as worn-out bearings, loose components, or electrical problems. These issues can lead to malfunctions that put operators at risk.
Regular maintenance is essential for ensuring the safe operation of lathes. This includes inspecting the machine for signs of wear and tear, lubricating moving parts, and replacing damaged components. Operators should also be trained to recognize the signs of potential mechanical failure and report them immediately.
Safety Measures for Lathe Operators
Preventing lathe accidents requires a combination of proper training, adherence to safety protocols, and the use of appropriate equipment. Below are some key safety measures that operators should follow:
- Wear Proper PPE: This includes safety goggles, gloves, and fitted clothing to prevent entanglement.
- Inspect the Machine: Before starting the lathe, operators should inspect it for any signs of damage or malfunction.
- Secure the Workpiece: Ensure that the workpiece is properly secured to prevent it from coming loose during operation.
- Use the Right Tools: Always use tools that are in good condition and appropriate for the task.
- Follow Safety Guidelines: Adhere to all safety protocols and guidelines provided by the manufacturer.
By following these measures, operators can significantly reduce the risk of accidents and ensure a safer working environment.
Case Studies of Lathe Accidents
Examining real-life case studies of lathe accidents can provide valuable insights into the causes and consequences of these incidents. One notable case involved an experienced operator who failed to secure the workpiece properly. As a result, the workpiece broke loose and struck the operator, causing severe injuries.
Another case involved a novice operator who neglected to wear proper PPE. During the operation, a piece of metal debris struck the operator in the eye, resulting in permanent vision loss. These examples underscore the importance of following safety protocols and using appropriate equipment.
Legal and Industrial Implications
Lathe accidents can have significant legal and industrial implications. In many cases, companies may face lawsuits or fines if it is determined that they failed to provide a safe working environment. Additionally, these accidents can lead to increased scrutiny from regulatory agencies, resulting in stricter safety standards and inspections.
From an industrial perspective, lathe accidents can disrupt operations, lead to lost productivity, and damage a company's reputation. Preventing these incidents is not only a matter of safety but also a sound business practice.
Preventive Measures and Training
Preventing lathe accidents requires a proactive approach that includes comprehensive training and the implementation of preventive measures. Operators should receive thorough training on machine operation, safety protocols, and emergency procedures. Regular refresher courses can help reinforce these lessons and keep safety top of mind.
In addition to training, companies should invest in safety equipment and technologies that can help reduce the risk of accidents. This includes installing safety guards, using automated systems, and implementing real-time monitoring tools.
The Role of Technology in Safety
Advancements in technology have played a significant role in improving safety in industrial environments. For example, modern lathes often come equipped with safety features such as emergency stop buttons, automatic shut-off systems, and sensors that detect potential hazards.
Companies can also leverage data analytics and machine learning to predict and prevent accidents. By analyzing data from past incidents, they can identify patterns and implement targeted interventions to reduce the risk of future accidents.
Conclusion and Call to Action
In conclusion, Russian lathe accident videos serve as a stark reminder of the dangers associated with operating industrial machinery. While these videos may be shocking, they also provide valuable lessons on the importance of safety and risk management. By understanding the causes of lathe accidents and implementing effective safety measures, we can prevent these incidents and ensure a safer working environment for everyone.
We encourage you to share this article with your colleagues and peers to raise awareness about the risks of lathe operations and the importance of safety. If you have any questions or would like to learn more about workplace safety, please feel free to leave a comment below. Together, we can make a difference and create a safer future for all.
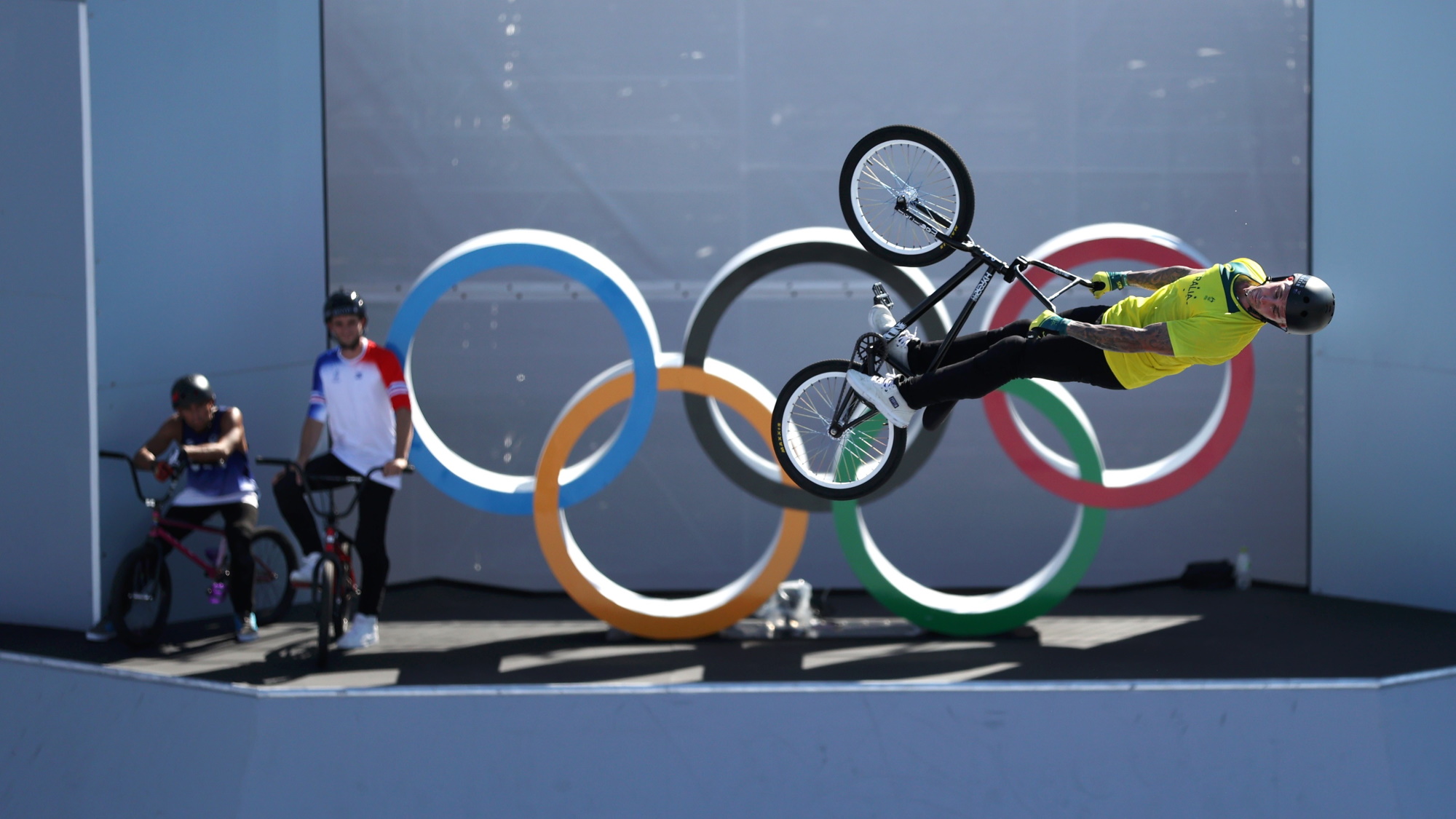